-
Ogłoszenia
-
Zostań naszym fanem. Obserwuj nas w social mediach : ) 12/11/2016
Daj się poznać jako nasz fan oraz miej łatwy i szybki dostęp do najnowszych informacji poprzez swój ulubiony portal społecznościowy. Obecnie można nas znaleźć m.in tutaj: Facebook: http://www.facebook.com/pages/Historiaorgp...19230928?ref=ts Twitter: http://twitter.com/historia_org_pl Instagram: https://www.instagram.com/historia.org.pl/ -
Przewodnik użytkownika - jak pisać na forum 12/12/2016
Przewodnik użytkownika - jak pisać na forum. Krótki przewodnik o tym, jak poprawnie pisać i cytować posty: http://forum.historia.org.pl/topic/14455-przewodnik-uzytkownika-jak-pisac-na-forum/
-
Zaloguj się, aby obserwować tę zawartość
Obserwujący
0
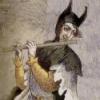
Wytop żelaza w prehistorii
Przez
Tomasz N, w Katalog artykułów historycznych użytkowników